The gypsum is sent to the packing silo through bucket elevator and screw conveyor.
Chemical additives and other raw materials were sent to the batch bin through the electric hoist.
The batching in all the stocks uses the metering screw conveyor which adjusts speed by using inverter and finishes feeding by step less speed.
During production, it will input set formula to the host computer according to the varieties and specifications. Based on the formulation requirements, large amount of construction gypsum was added to the mixer after measured by measurement scale number 1, small amount of materials were added to the mixer after measured by measurement scale number 2. The measurement scale in this project uses dosage method.
The materials will unload to the middle silo after mixing in the mixer.
The building gypsum after mixing is packaged by packing machine (adopt automatic sealing bag), and then delivered into finished product library. The packing machine adopts feedback signal of pressure sensor for controlling the charging of screw feeder. The packing machine will stop to load materials when the weight of materials reaches set value. Next the pounding machine will reshape it as standard shape. Finally the computer-controlled inkjet printing machine will print automatically on the surface of bag which includes date of manufacture, manufacturer, trademark, etc..
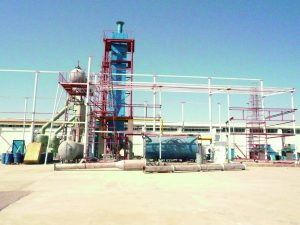
The gypsum is sent to the packing silo through bucket elevator and screw conveyor.
Chemical additives and other raw materials were sent to the batch bin through the electric hoist.
The batching in all the stocks uses the metering screw conveyor which adjusts speed by using inverter and finishes feeding by step less speed.
During production, it will input set formula to the host computer according to the varieties and specifications. Based on the formulation requirements, large amount of construction gypsum was added to the mixer after measured by measurement scale number 1, small amount of materials were added to the mixer after measured by measurement scale number 2. The measurement scale in this project uses dosage method.
The materials will unload to the middle silo after mixing in the mixer.
The building gypsum after mixing is packaged by packing machine (adopt automatic sealing bag), and then delivered into finished product library. The packing machine adopts feedback signal of pressure sensor for controlling the charging of screw feeder. The packing machine will stop to load materials when the weight of materials reaches set value. Next the pounding machine will reshape it as standard shape. Finally the computer-controlled inkjet printing machine will print automatically on the surface of bag which includes date of manufacture, manufacturer, trademark, etc..