이름: | 파리 식물의 석고 | 연간 용량: | 30000-500000 톤/년 |
---|---|---|---|
소성 시스템: | 고취 된 용광로, 로타리 가마, 주전자 | 연료 유형: | 석탄, 천연 가스, 기름, 등 |
원료: | 석고 록/광산 | 사일로: | 구매자가 제공합니다 |
설치: | 우리는 설치 안내를 위해 기술자를 사이트로 보내드립니다. | 제어 시스템: | PLC 제어 |
완제품 사용: | 건축을위한 건축 자재 | 애프터 판매 서비스: |
분쇄 분말 공정 또는 분말 사일로에서 생성된 분말 재료, 그들은 수직을 통해, 수평 컨베이어를 거친 다음 측정 스크류 컨베이어를 통해 하소를 위한 비등로로 들어갑니다.. 끓는로는 고온의 열전달 오일을 열원으로 사용합니다., 고온 열전달 오일은 석탄 화력 오일 보일러에 의해 제공됩니다.. 고온의 이송 오일이 끓는로에 들어갈 때, 열교환기에 의해 열이 석고분말로 전달됩니다., CaSO4 *2H2O를 CaSO4 *1/2H2O로 변환 (석고 건축). 소성 중, 원료석고 투입량에 따라 토출온도를 조절합니다., 소성 건물 석고 비등로에서 연속 자동 배출, 스크류 컨베이어와 버킷 엘리베이터를 거쳐 건물 석고 사일로로 이송됩니다.. 그리고 열전달 오일은 재가열을 위해 석탄 화력 열유 보일러로 흐름을 반환합니다..
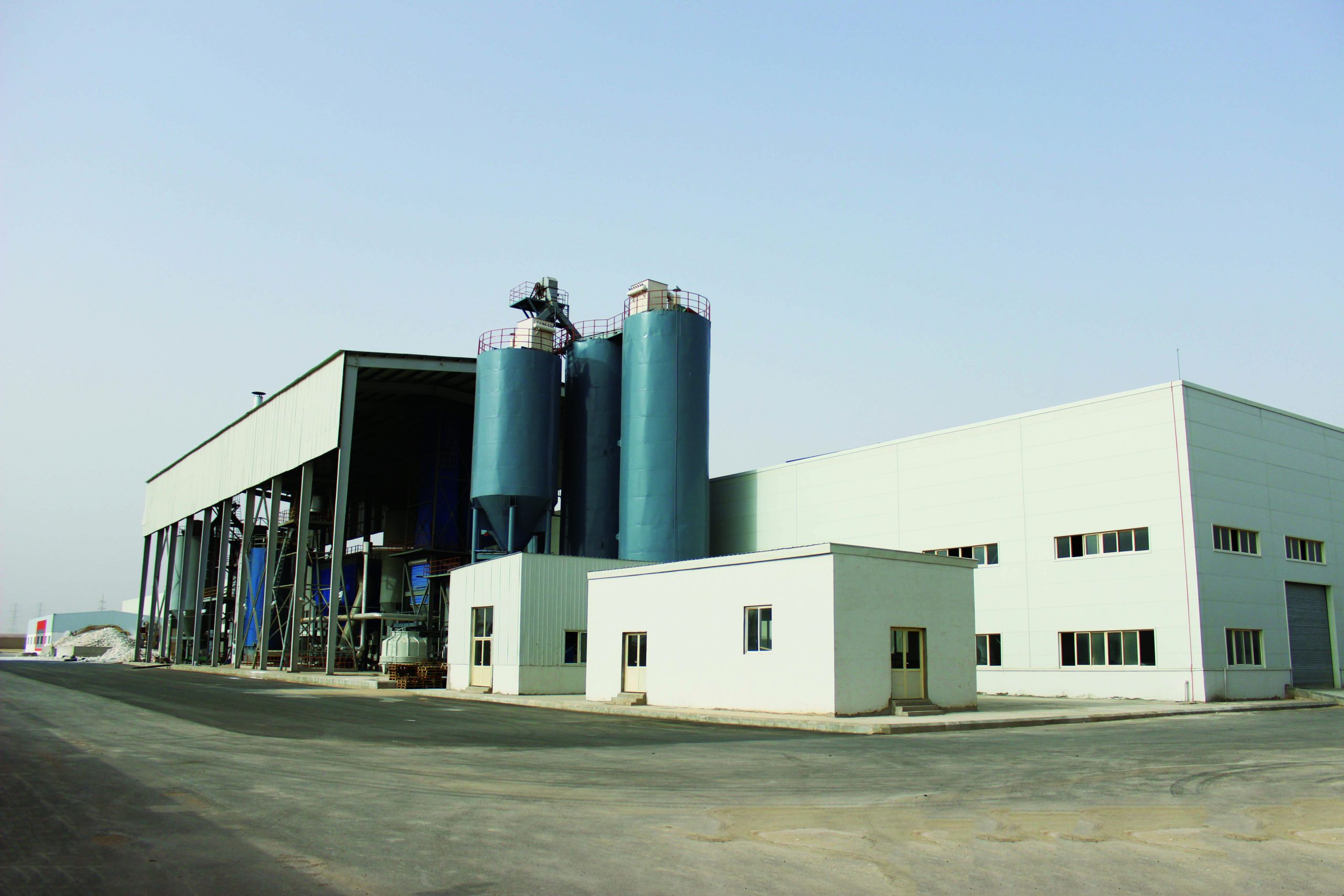
석고 기계
자연 석고의 간단한 소개
천연 디 하이드레이트 석고 (CASO4 · 2H2O) Raw 석고라고도합니다. 소성 및 연삭 후, β hemihydrate 석고 (CASO4 · H2O), 그게, 석고 건축, 파리의 석고와 라임 머드로도 알려져 있습니다.. 석고 광산은 주로 퇴적물 퇴적물로 구성됩니다, 그리고 매장량은 그 이상을 차지합니다 90% 나라의. 후성 유전 학적 및 열수 변성 석고 광산은 그다지 중요하지 않습니다.. 석고 광산은 모든 연령대에서 생산되었습니다, 초기 백악기 및 3 차 퇴적 석고 퇴적물이 가장 중요합니다..
가장 널리 사용되는 천연 석고는 이수대 석고입니다, 활성 성분은 황산 칼슘 이수수입니다. 일반적으로, 석고는 광석의 황산 칼슘 이수수의 함량에 따라 등급이 매겨집니다.. 석고에는 광범위한 응용 분야와 다양한 유형의 제품이 있습니다.. 다른 사용법은 석고 원료의 품질에 대한 요구 사항이 다릅니다.. 고급 석고는 주로 Edible과 같은 특수 석고 제품 생산에 사용됩니다., 의료, 미술, 모델 및 화학 필러, 등.; 황산 칼슘 함량이 적은 석고 광석 60% 거의 사용되지 않습니다; 이상 60% 석고 광석은 건축 자재 및 건축 등과 같은 다양한 분야에서 사용됩니다., 그 내용에 따라.
천연 석고 분말 생산 라인의 용량
톤/년 | 톤/시간 | 석고 석재 소비 톤 / 년도 | 가열 매체
|
열 자원 |
20,000 | 2.78 | 24,000 | 열유, 열기, 증기 |
석탄, 천연 가스, 가벼운 오일, 중유, 바이오 매스, 증기 |
30,000 | 4.12 | 36,000 | ||
40,000 | 5.56 | 48,000 | ||
60,000 | 8.24 | 72,000 | ||
80,000 | 11.11 | 96,000 | ||
100,000 | 13.88 | 120,000 | ||
150,000 | 20.83 | 180,000 | ||
200,000 | 27.78 | 240,000 | ||
30,0000 | 41.66 | 360,000 |
자연 석고 생산 공정 설명
석고 석재는 원료 파일에서 로더에 의해 강철 호퍼를받는 재료로 보내집니다., 그리고 큰 석고 석재는 분쇄기에 의해 분쇄되어 공정의 필요한 입자 크기에 도달합니다., 입자 크기의 요구 사항을 충족하는 재료는 운송 장치를 통해 원료 저장 사일로에 저장됩니다.. 작은 재료는 분쇄를 위해 밀로 계량하여 운송됩니다., 그리고 블록 재료는 공정의 필요한 미세에 도달하기 위해 제 분소의 분말로 접지 될 것입니다.. 파우더는 버퍼링을 위해 운송 장치를 통해 버퍼 사일로로 운반됩니다.. 그 다음에, 분말은 계량 공급 장치를 통해 석고 분말 소환 장비로 균일하게 전달됩니다., 그리고 석고 분말은 이화물 석고를 반 세미드 석고로 전환 할 것입니다.. 소액화가 완료된 후, 볼 밀에 의해 수정됩니다, 쿨러에 의해 냉각되었습니다 , 그리고 저장 및 노화를 위해 운송 장비를 통해 완제품 창고로 운송.